How Wearables and Vibration Sensors Enhance Predictive Maintenance in the Oil & Gas Industry
Discover how combining wearables like iSmarch’s LoRaWAN smartwatch J3 and HM01 helmet with vibration and pressure sensors optimizes predictive maintenance in the oil and gas industry. Learn about sensor options, wearable benefits, and how integrating these technologies enhances safety, efficiency, and cost savings.
جدول المحتويات
The Need for Predictive Maintenance in Oil & Gas
In the oil and gas industry, where equipment operates under high pressure and extreme conditions, predictive maintenance is essential for ensuring safe, efficient, and uninterrupted operations. Traditional preventive maintenance practices, although helpful, often lead to over-maintenance or missed failure predictions, which can increase costs and risk unplanned downtime. Predictive maintenance, on the other hand, leverages advanced sensor technology and data analytics to monitor the real-time condition of machinery, allowing maintenance teams to predict failures before they happen and service equipment only when needed.
Predictive maintenance is not only about preventing unexpected breakdowns but also about optimizing the overall operational efficiency and extending the lifespan of critical equipment, from compressors and pumps to drilling machinery and pipelines. As more companies look to digitalize their maintenance practices, smart wearables و vibration sensors are becoming key players in a connected maintenance ecosystem that keeps both equipment and workers safe.
In this context, vibration and pressure sensors serve as the foundational technology for predictive maintenance. They provide crucial data on equipment health and performance by measuring variations in vibration patterns, pressure levels, temperature fluctuations, and other key indicators. These sensors detect early signs of wear and tear or abnormal conditions, sending real-time alerts for potential issues before they escalate into costly failures.
At the same time, smart wearables such as iSmarch’s LoRaWAN smartwatch J3 and helmet HM01 offer an innovative approach to support and enhance predictive maintenance processes by monitoring worker health, location, and environmental conditions. When combined with traditional sensors, wearables provide an additional layer of safety and operational insight, bridging the gap between human-centric and machine-centric data.
Overview of Sensor Types and Key Functions
Predictive maintenance relies heavily on vibration and pressure sensors to track equipment health and identify potential issues early. Selecting the right sensors for the job is essential, as these sensors provide the foundational data that informs maintenance decisions and keeps operations running smoothly.
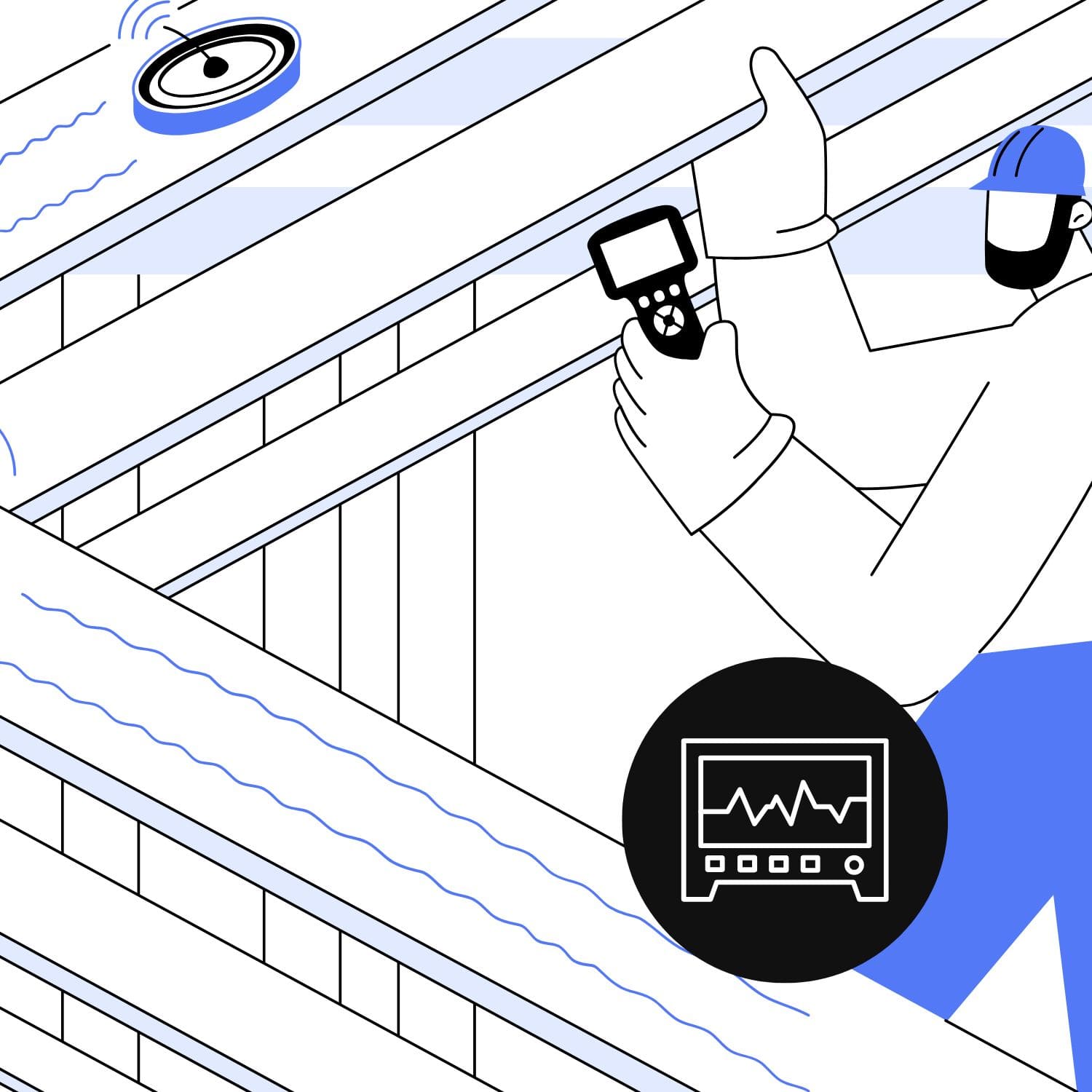
Vibration Sensors
الغرض: Vibration sensors are used to detect changes in the vibration patterns of rotating equipment, such as pumps, motors, and compressors. Changes in vibration amplitude, frequency, or pattern can indicate issues like misalignment, imbalance, bearing wear, or mechanical looseness.
Types:
- Accelerometers: The most common type of vibration sensor, accelerometers measure changes in acceleration, providing highly accurate data on vibration intensity.
- Velocity Sensors: Useful for measuring medium-frequency vibrations, often preferred for monitoring larger machinery where velocity measurements are more relevant.
- Displacement Sensors: Used for low-frequency vibrations, displacement sensors are especially effective in monitoring heavy, slow-moving machinery or structural components.
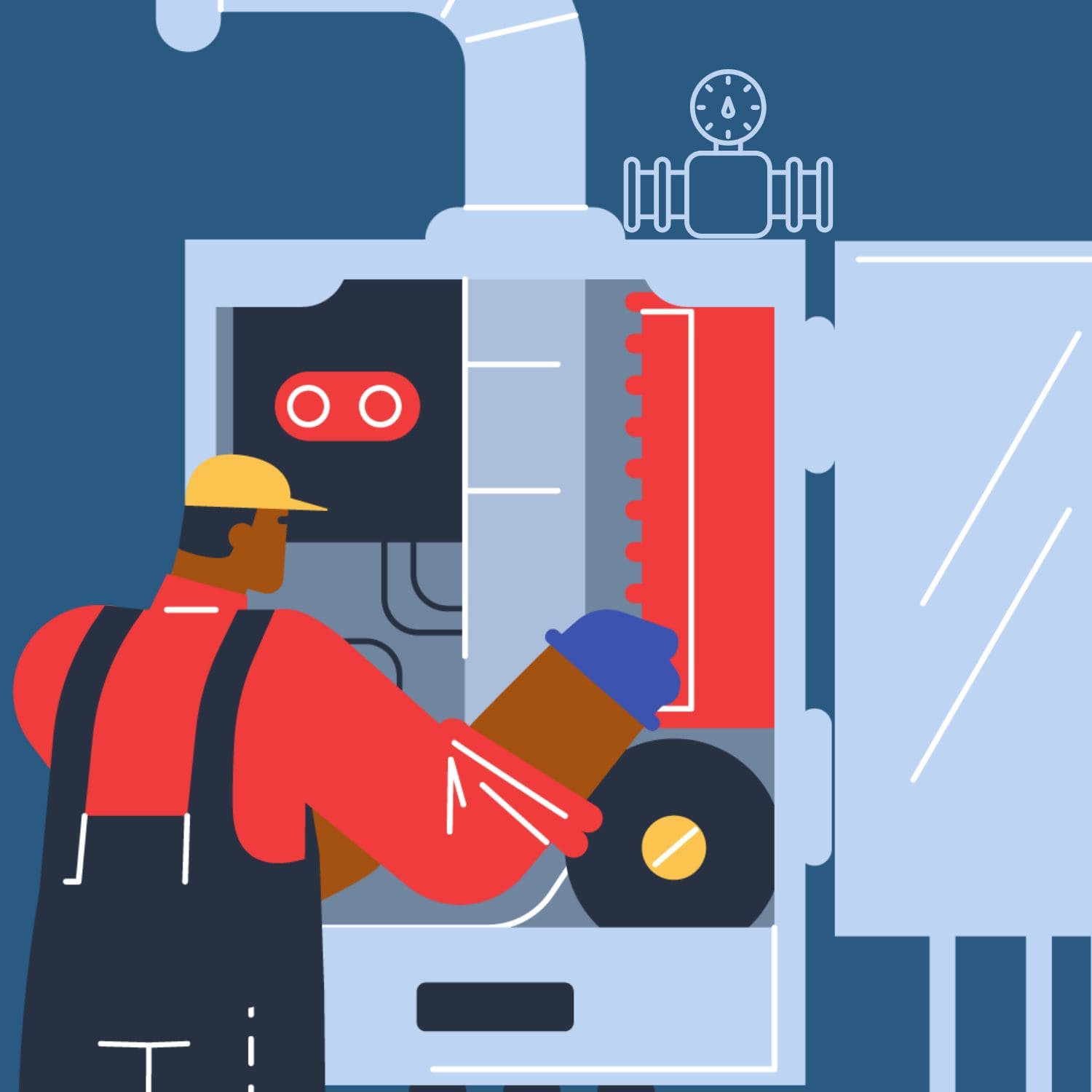
Pressure Sensors
الغرض: Pressure sensors monitor changes in pressure within pipelines, compressors, or storage tanks. Pressure deviations may indicate leaks, blockages, or changes in fluid flow, all of which require immediate attention.
Types:
- Absolute Pressure Sensors: Measure pressure against a vacuum, commonly used in applications where pressure stability is critical.
- Gauge Pressure Sensors: Measure pressure relative to atmospheric pressure, often used in tank level monitoring and flow systems.
- Differential Pressure Sensors: Measure the difference between two points, typically in pipelines or filtration systems, to identify flow disruptions or system inefficiencies.
Top Vibration and Pressure Sensor Brands for the Oil & Gas Industry
When selecting vibration and pressure sensors, reliability and precision are paramount, especially in an industry with high safety and regulatory standards. Below are some of the top brands known for delivering high-quality sensors suited for the oil and gas industry
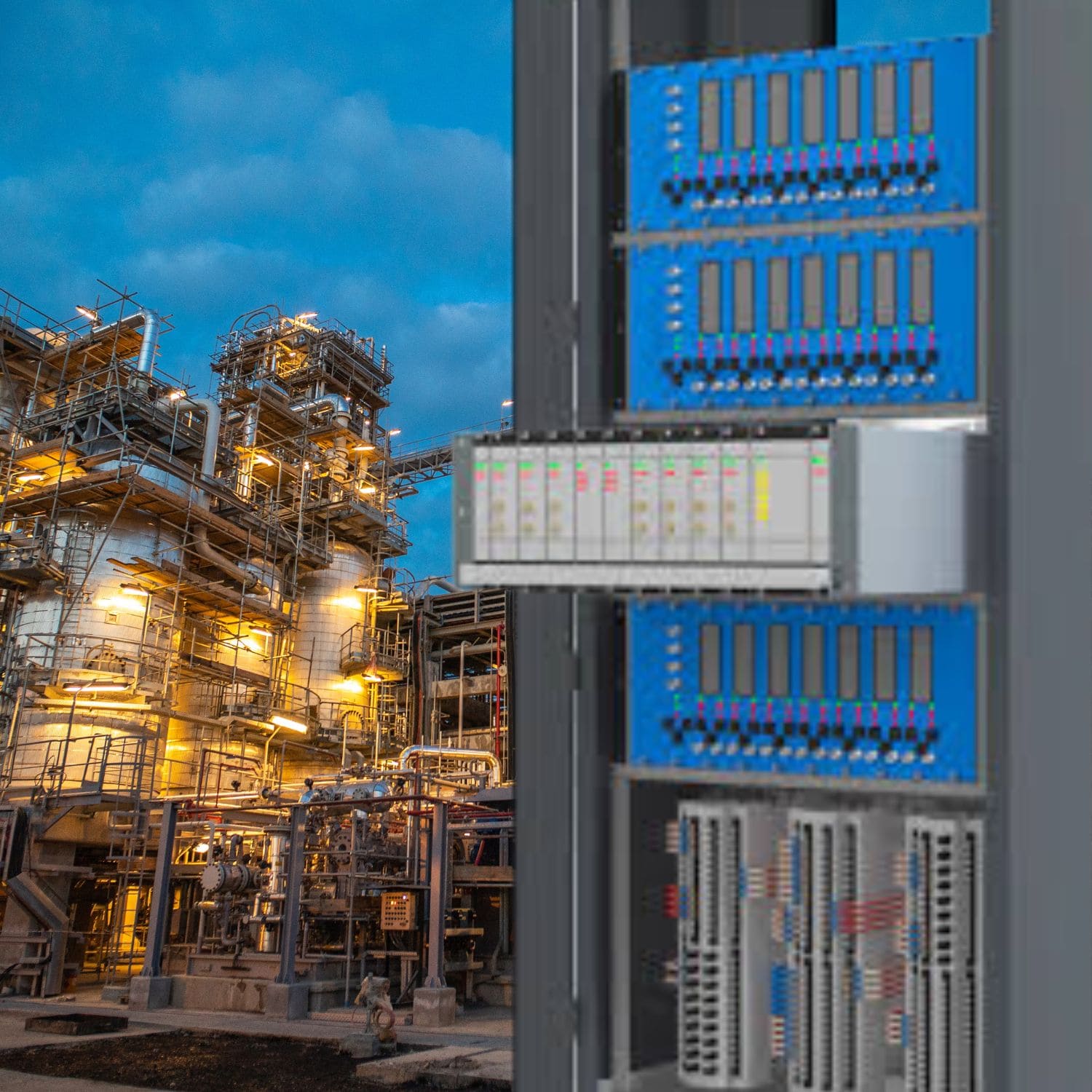
Emerson
Offers a wide range of vibration and pressure sensors, including their renowned AMS 6500 ATG vibration monitoring system for critical rotating machinery. Known for high accuracy and durability, Emerson’s sensors are widely used for both stationary and remote applications in harsh environments.
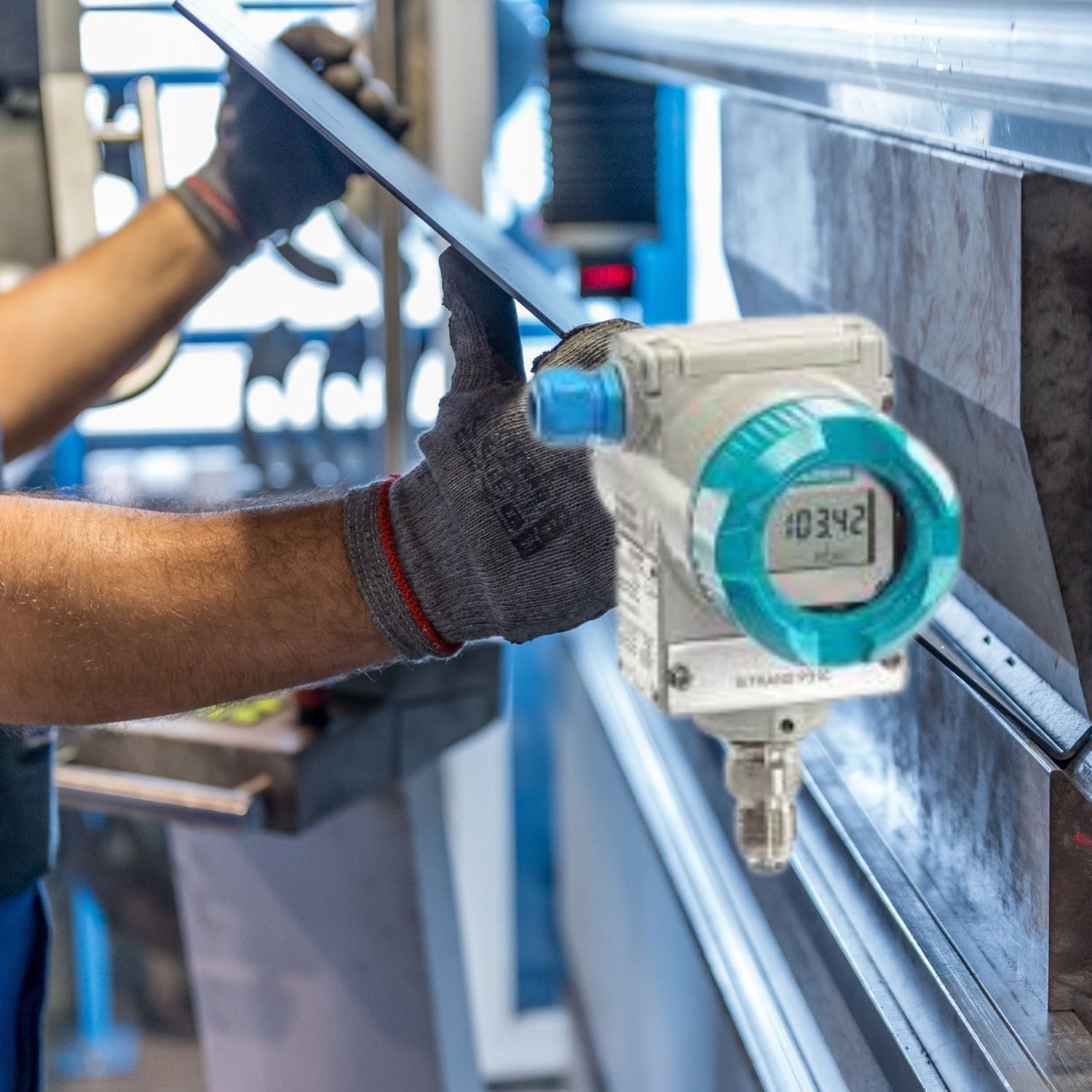
Siemens
Siemens provides vibration and pressure sensors that integrate seamlessly into industrial IoT systems. The Siemens Sitrans P series is especially popular for pressure measurement, known for its precision and rugged design, making it ideal for both offshore and onshore applications.
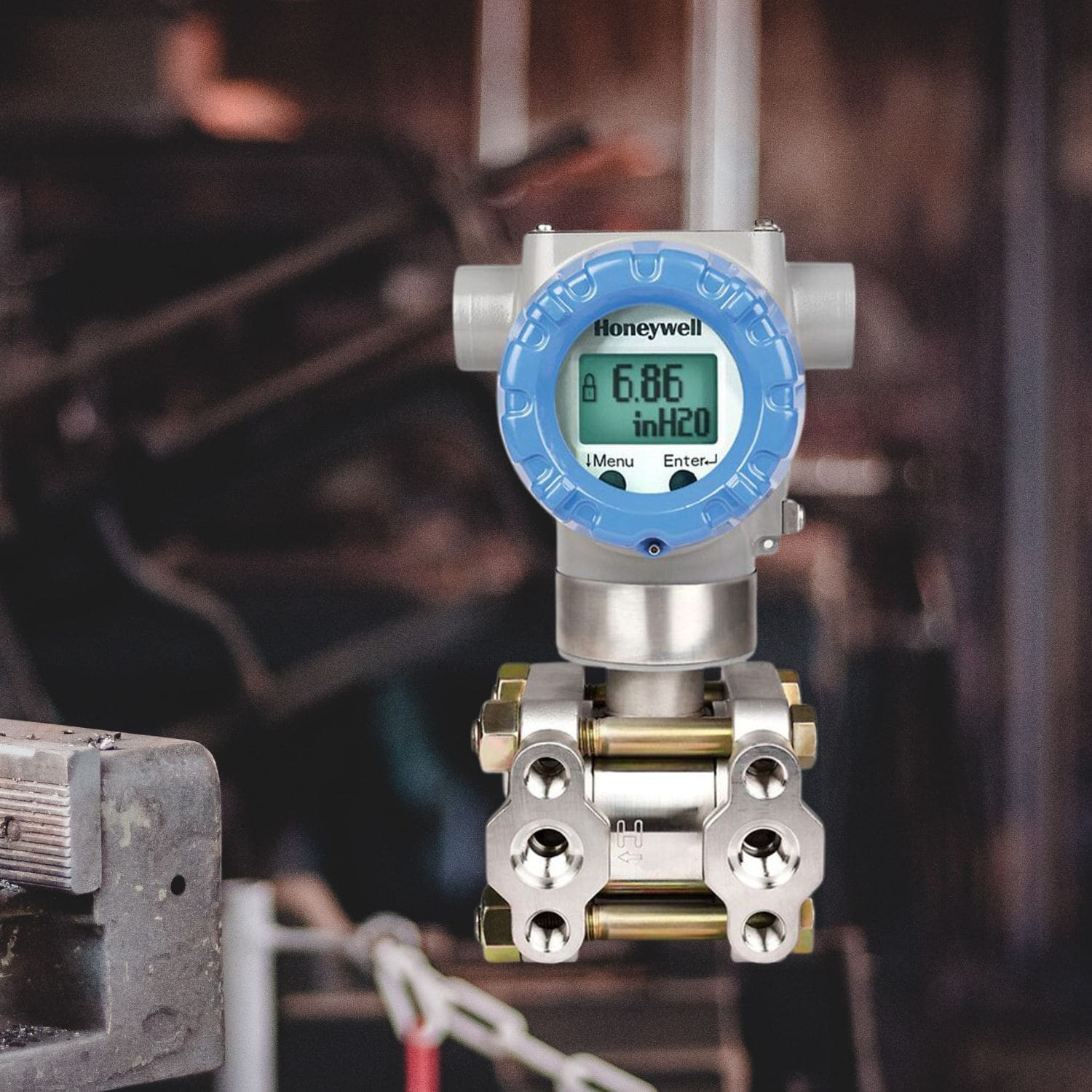
Honeywell
Honeywell is known for its robust and reliable SmartLine pressure transmitters and vibration sensors that provide high-quality, accurate data essential for critical applications in oil and gas. They offer scalable solutions that allow for integration with advanced predictive maintenance software.
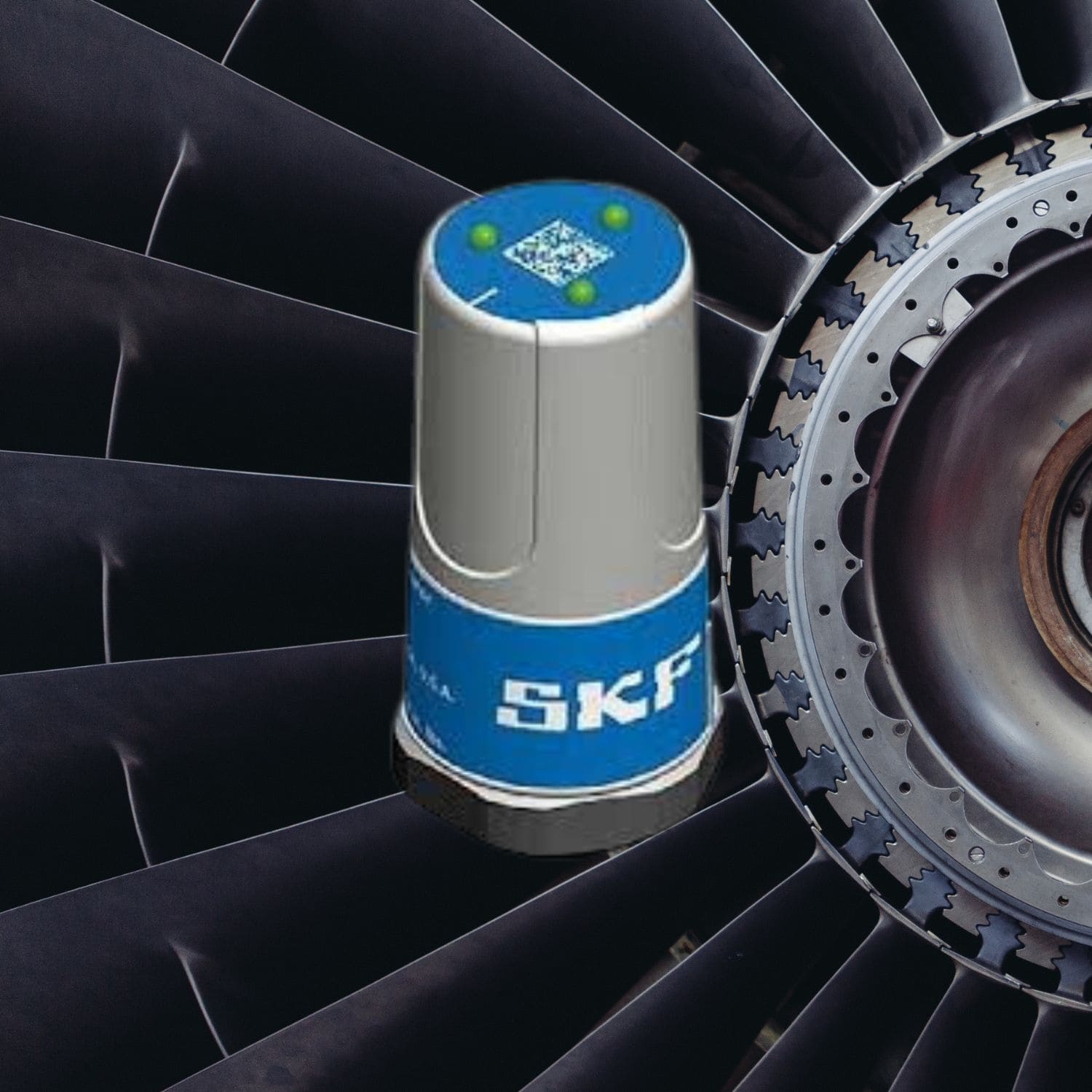
SKF
Specializing in vibration sensors, SKF’s CMSS series is well-regarded for high sensitivity and wide frequency response. Their sensors are optimized for rotating machinery in extreme conditions, often preferred for monitoring pumps, motors, and other key assets in oil and gas.
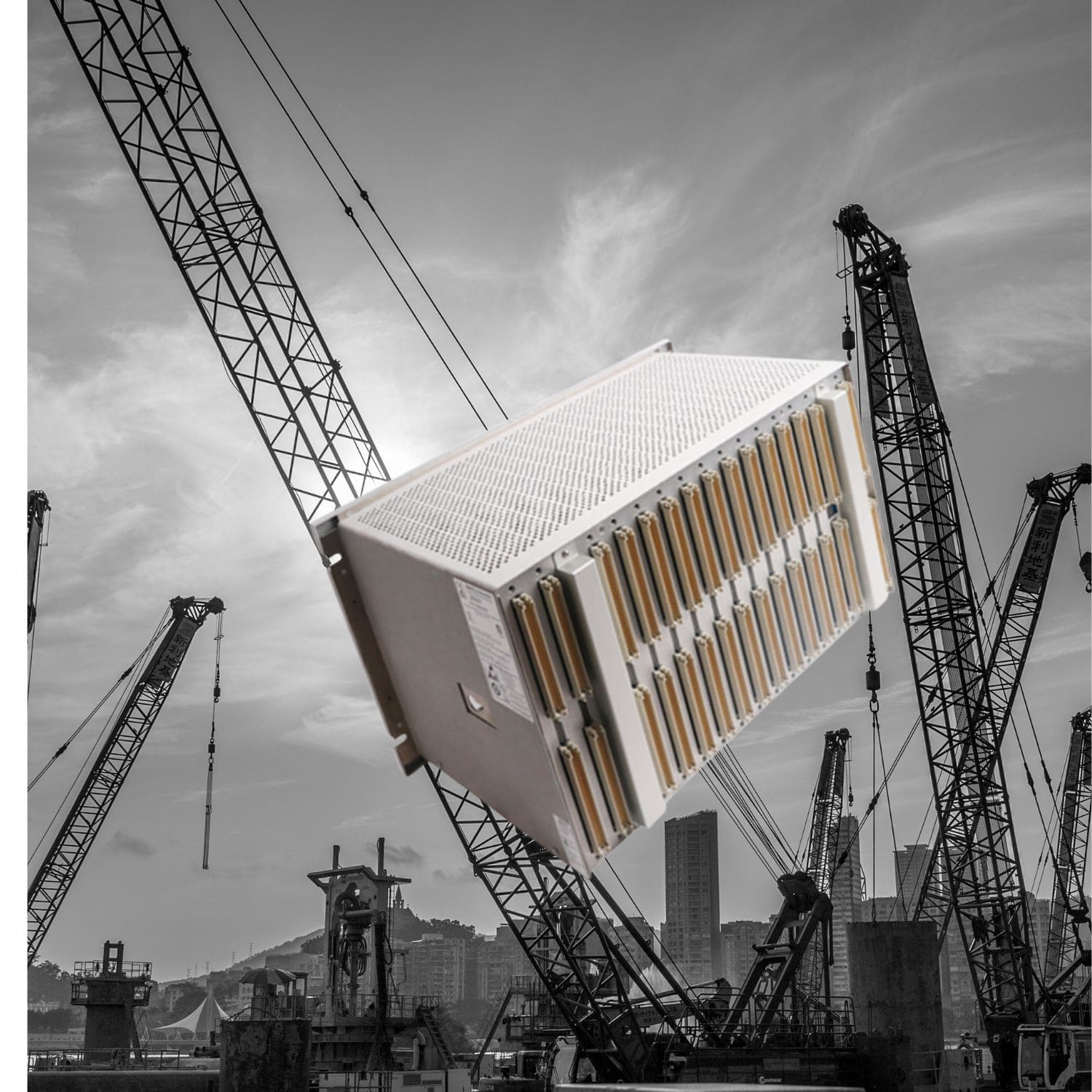
Bently Nevada by Baker Hughes
Bently Nevada is a leader in vibration monitoring solutions, especially known for its 3300 and 3500 Series for heavy-duty industrial applications. Their sensors are trusted for high-precision monitoring, making them a go-to choice for gas turbines, compressors, and rotating equipment.
How to Choose the Best Sensors for Your Project
Selecting the right sensors requires understanding the specific needs of your predictive maintenance goals, as well as the environment in which the sensors will operate. Here are a few key factors to consider
1. Operating Environment
- Temperature: Oil and gas equipment often operates in extreme temperatures, so choose sensors that can withstand high heat or cold.
- Humidity and Corrosion Resistance: For offshore or high-humidity environments, sensors need to be corrosion-resistant and waterproof.
- Hazardous Zone Certification: Many oil and gas facilities are classified as hazardous zones, requiring sensors with ATEX or similar certifications.
2. Sensor Compatibility and Connectivity
- Ensure sensors are compatible with your existing IoT and maintenance systems. Many modern sensors offer LoRaWAN أو Bluetooth connectivity, enabling wireless communication and real-time monitoring.
- Look for sensors that can integrate easily with both traditional and digital systems, allowing for future scalability and flexibility.
3. Measurement Precision and Data Output
- The level of precision required will depend on the criticality of the equipment being monitored. High-precision sensors are essential for critical assets, while less sensitive sensors may suffice for non-critical machinery.
- Ensure sensors provide data output that can be seamlessly fed into your predictive maintenance analytics software.
4. Supplier Support and Maintenance
- Choose a supplier known for robust customer support, especially one that provides technical support, training, and software updates. Leading brands like Emerson and Honeywell often offer extended service contracts, which can be valuable for long-term operations.
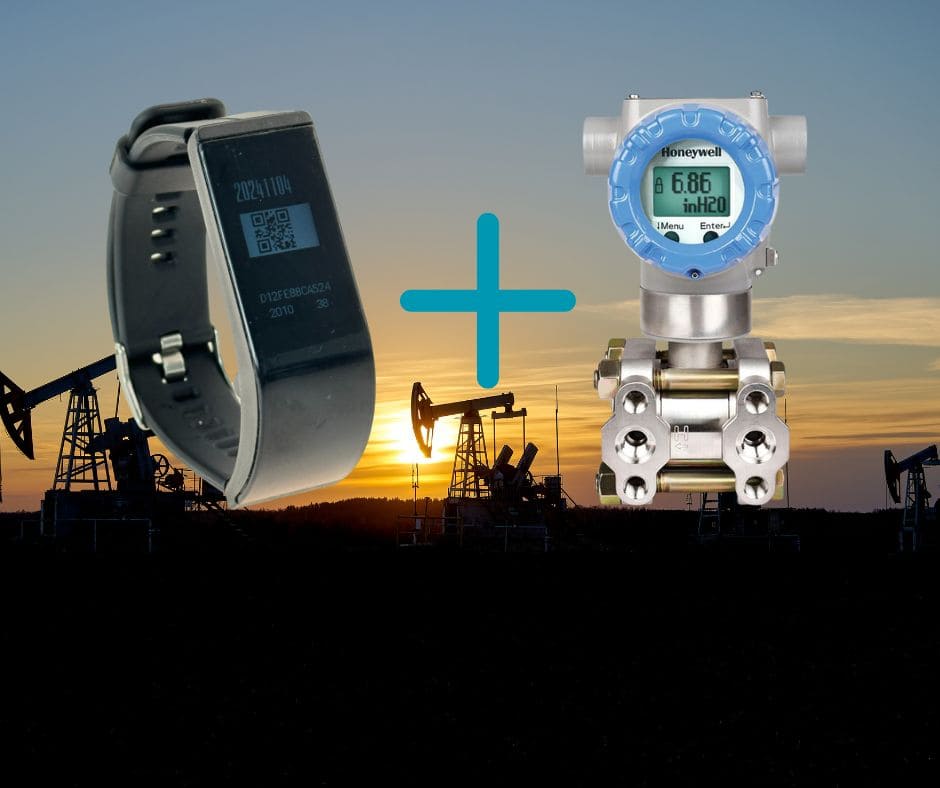
The Synergy of Smart Wearables with Vibration and Pressure Sensors
As predictive maintenance becomes increasingly data-driven, integrating smart wearables with traditional vibration and pressure sensors can unlock new levels of safety, efficiency, and operational insight. While vibration and pressure sensors provide critical information about machinery health, smart wearables add a human-centric layer by monitoring worker health, and proximity to equipment. Together, these technologies create a connected maintenance ecosystem where both equipment and worker safety are continuously managed.
How Smart Wearables and Sensors Work Together for Optimal Predictive Maintenance
When used in tandem, wearables and sensors form an interconnected network that provides comprehensive, real-time insights. Here’s how they interact:
Data Flow and Real-Time Alerts
Machinery sensors continuously monitor vibration and pressure data, detecting anomalies that might indicate impending issues. When an anomaly is detected, a signal is sent to smart wearables, alerting nearby workers of potential hazards.
Worker Location and Safety Monitoring
Wearables track worker locations, ensuring that maintenance personnel are clear of high-risk zones when critical maintenance is scheduled. If a worker is near a machine that requires maintenance, the system can delay or reschedule the activity to prioritize worker safety.
Environmental Data Integration with Smart Wearables as a Hub
Although smart wearables like the iSmarch J3 smartwatch do not include built-in environmental sensors, they can function as hubs, receiving data from nearby environmental sensors that monitor factors such as gas levels, temperature, or humidity. This integration enables workers to receive alerts on their smartwatches if environmental sensors detect hazardous conditions, ensuring safety and providing a holistic view of the work environment.
Key Benefits of Combining Smart Wearables with Vibration, Pressure, and Environmental Sensors
The combined use of wearables and sensors brings multiple advantages to predictive maintenance operations
Enhanced Predictive Analytics
- The combination of machinery data from sensors and worker data from wearables allows for more accurate predictive analytics. For instance, an increase in vibration levels combined with environmental hazards detected by external sensors can highlight areas needing urgent attention.
- This synergy enhances the reliability of predictive models, helping maintenance teams prioritize issues based on both equipment health and environmental risks.
Improved Safety and Efficiency
- Wearables provide instant alerts to maintenance workers, ensuring they’re aware of any equipment abnormalities that may affect safety. This real-time feedback loop minimizes the risk of accidents and enables faster, more efficient responses to machinery issues.
- Vibration sensors can trigger maintenance alerts to wearables when machinery shows signs of overheating or abnormal vibration, allowing workers to address the issue before it escalates.
Optimized Maintenance Workflow
- Combining wearables and sensors enables smarter scheduling for maintenance tasks, ensuring workers are deployed to the right areas with the right precautions. For example, if a piece of equipment requires attention in a hazardous zone, data from wearables and environmental sensors can verify that workers enter the area only when conditions are safe.
- This level of coordination reduces unnecessary inspections and allows maintenance teams to focus on areas with verified issues, streamlining the maintenance process and improving uptime.
Real-World Applications in Oil & Gas
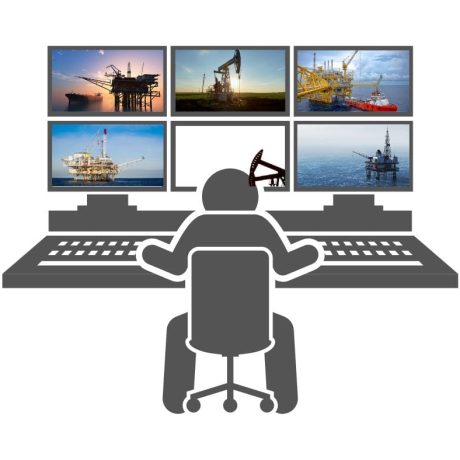
Oil Rig Monitoring
Wearables help track worker health and location, while vibration sensors monitor the health of critical equipment. If a sensor detects abnormal vibration in a pump, the system can notify nearby workers to evacuate the area or conduct a safe inspection.
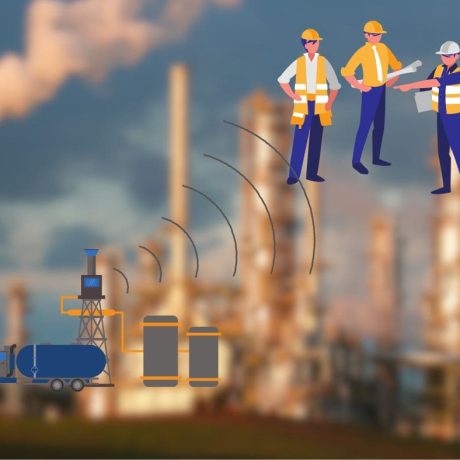
Pipeline Integrity Management
For pipelines, vibration and pressure sensors can detect leaks or blockages, while environmental sensors monitor conditions such as gas levels. The smartwatch acts as a hub, alerting workers through real-time notifications if any conditions become unsafe during inspection.
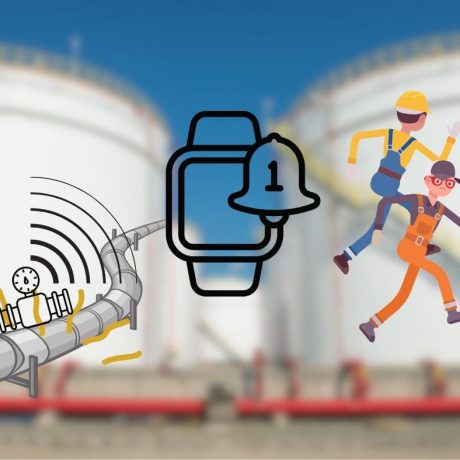
Refinery Safety Systems
In refineries, environmental sensors monitor gas levels or high temperatures. Workers receive notifications on their wearables if unsafe levels are detected, ensuring they stay informed of environmental hazards and are protected from equipment malfunctions.
Introducing iSmarch’s Smart Solutions for Oil & Gas: J3 LoRaWAN Smartwatch and Smart Helmet Attachment (VCT lnSite)
iSmarch brings cutting-edge wearable solutions specifically designed for high-risk industries like oil and gas. Our J3 LoRaWAN Smartwatch و Smart Helmet Attachment (VCT lnSite) offer robust health monitoring, connectivity, and safety features, making them ideal choices for companies looking to enhance their predictive maintenance systems while prioritizing worker safety.
Enhanced J3 LoRaWAN Smart Watch: A Fusion of Health and Connectivity
إن J3 LoRaWAN Smartwatch is engineered to meet the rigorous demands of the oil and gas industry, providing critical health data, real-time location tracking, and emergency support. By seamlessly uploading health metrics and GPS positioning data to the cloud through LoRa gateways, the J3 ensures that both worker well-being and safety are continuously monitored and managed in real time.
J3 Smartwatch Features
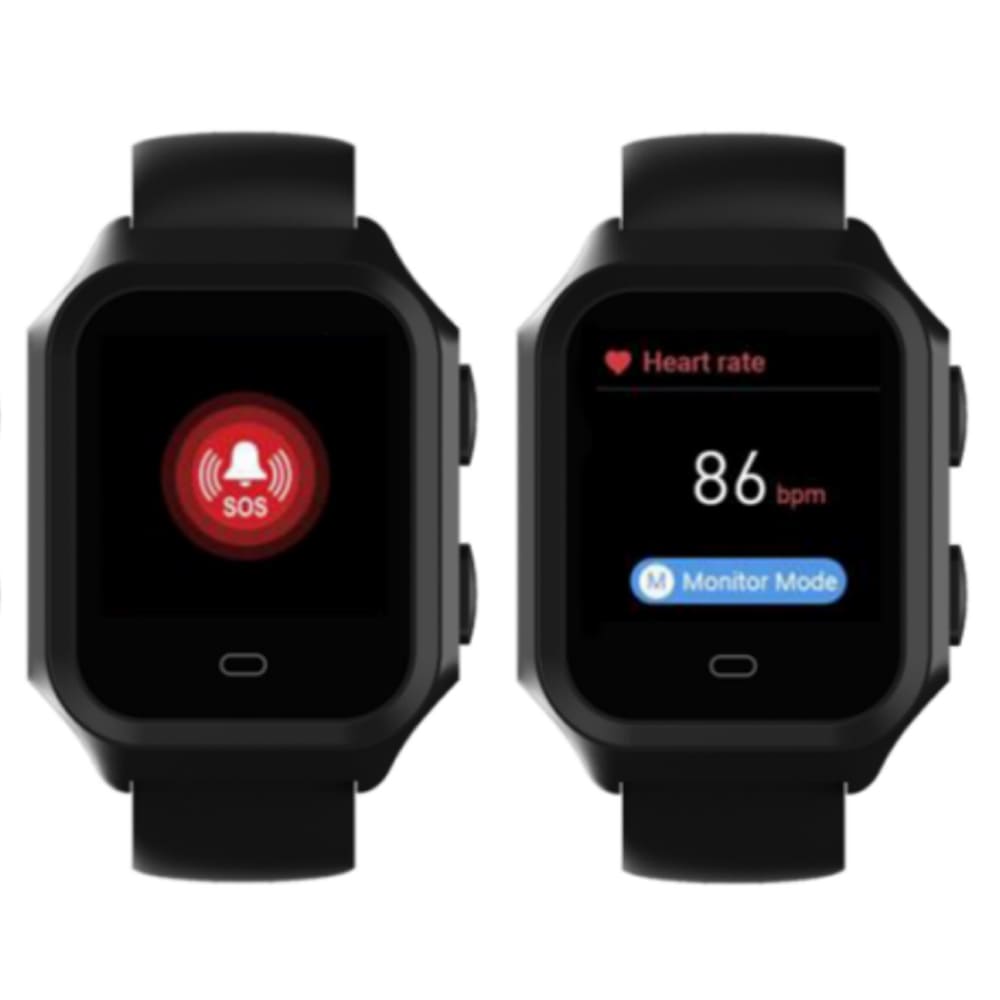
Advanced Blood Oxygen Tracking
The J3 smartwatch employs photoplethysmography (PPG) sensors to measure blood oxygen levels (SpO2) with red and infrared light for accurate readings—a critical feature for workers in high-altitude or confined spaces where oxygen levels may fluctuate.
Comprehensive Health Monitoring
Real-time body temperature monitoring, static and dynamic heart rate tracking, and blood pressure measurement ensure a comprehensive view of worker health, allowing supervisors to detect early signs of heat stress, fatigue, or other health issues.
Stress and Fatigue Analysis
Utilizing HRV data, the J3 smartwatch evaluates stress levels and fatigue, providing updates before work begins. This helps project managers ensure workers are ready to perform tasks safely and efficiently.
Activity Tracking and Emergency SOS Function
The J3 tracks activity levels and includes an SOS feature that workers can activate in emergencies, instantly alerting supervisors and connecting to the cloud for rapid response.
Built for Durability
The J3 smartwatch’s rugged, IP68-rated build and long-lasting battery make it resilient in harsh conditions, from high temperatures to heavy dust and water exposure, making it ideal for demanding oil and gas sites.
Connectivity and Data Management
- LoRaWAN and GPS Integration: The J3 sends continuous health and location updates to the cloud every five minutes, ensuring supervisors have up-to-date data on worker safety and location.
- Cloud-Ready for Predictive Maintenance Systems: The smartwatch serves as a central hub for receiving alerts from environmental sensors, vibration sensors, and more. It functions as part of a larger connected network that supports predictive maintenance by alerting workers of unsafe zones or maintenance needs in real-time.
Smart Helmet Attachment (VCT lnSite): Enhanced Safety Through Integrated Health Monitoring and Communication
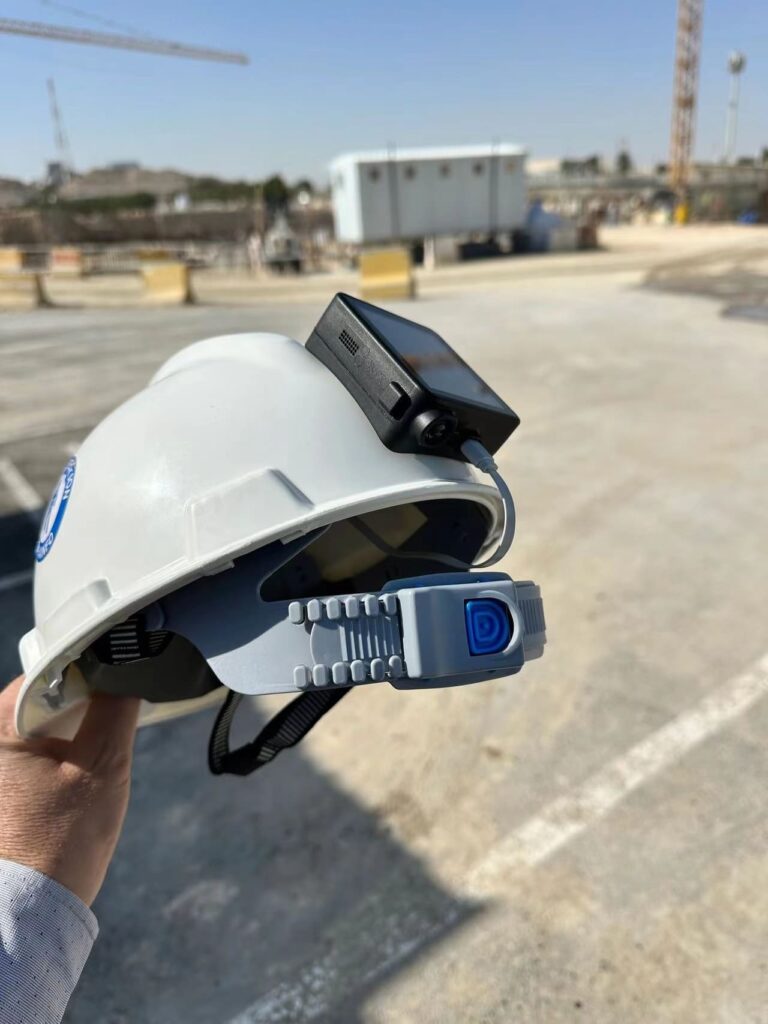
Solar-Powered for Extended Usage
With a durable solar panel, the attachment provides a sustainable power source, ensuring long operational periods even in remote sites with limited access to power.
Robust Health Monitoring
Equipped with sensors placed comfortably at the forehead, the attachment tracks vital signs such as heart rate, blood oxygen levels (SpO2), and body temperature, providing ongoing health insights.
Integrated Communication System
The helmet includes a built-in speaker system capable of playing pre-recorded messages in emergencies, allowing for immediate evacuation instructions or hazard alerts, ensuring worker safety in high-risk situations.
Head Movement and Attention Tracking
Sensors track head movement to monitor worker focus, attention levels, and any signs of potential distractions, reducing accident risks and improving productivity.
Durability and Comfort
Made from high-stress Matteris material, the helmet attachment is built to withstand challenging environments, from extreme temperatures up to 80°C to high-impact situations. It’s also water-resistant, ensuring reliable performance across diverse weather conditions.
Why Choose iSmarch’s Wearables for Oil & Gas Applications?
إن J3 LoRaWAN Smartwatch و VCT lnSite Helmet Attachment together provide a powerful, integrated approach to workplace safety and efficiency. In high-risk industries like oil and gas, where both worker safety and predictive maintenance are paramount, these devices offer a unique solution that enhances the connected maintenance ecosystem.
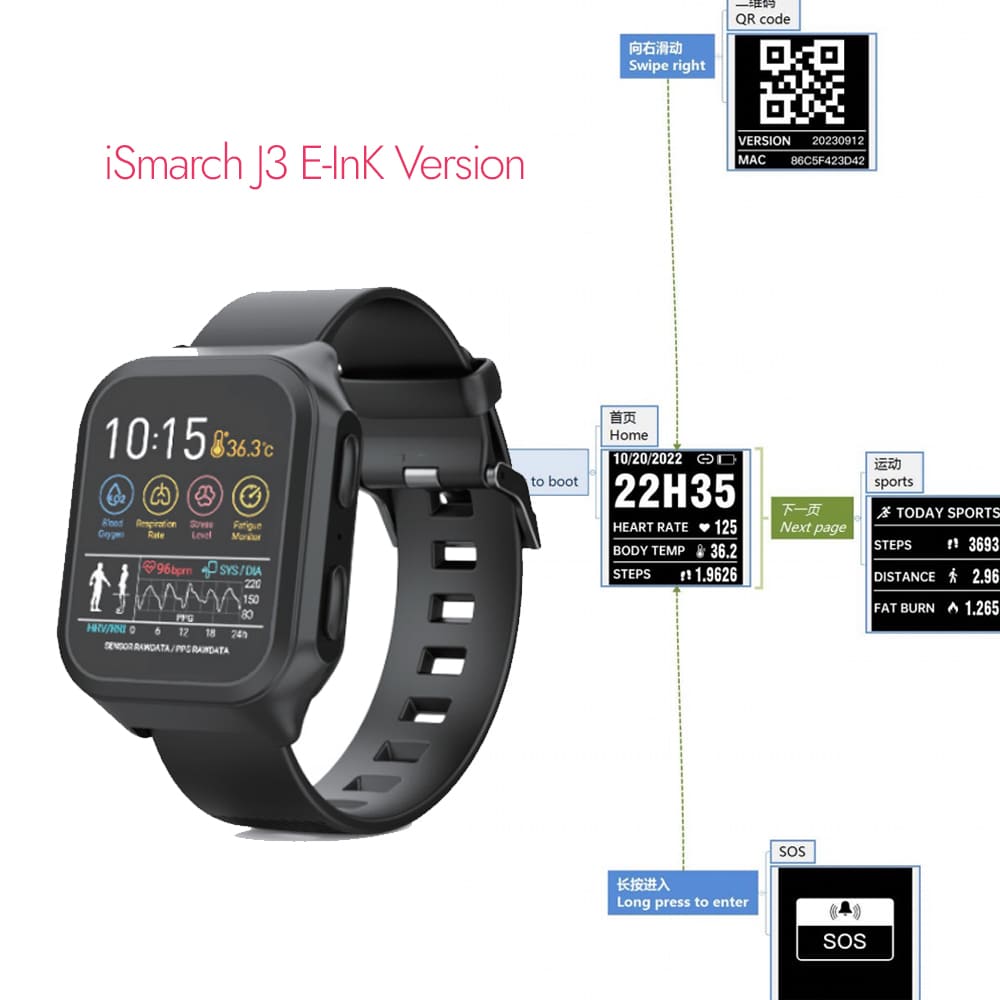
Seamless Integration with Predictive Maintenance
Both the J3 smartwatch and VCT lnSite helmet attachment serve as critical components in a predictive maintenance strategy, working alongside traditional sensors to deliver real-time data on worker health, location, and equipment status.
Enhanced Safety and Productivity
Through real-time health tracking, alerts, and project management integration, these devices ensure workers are protected and supervisors have the data needed to optimize safety protocols.
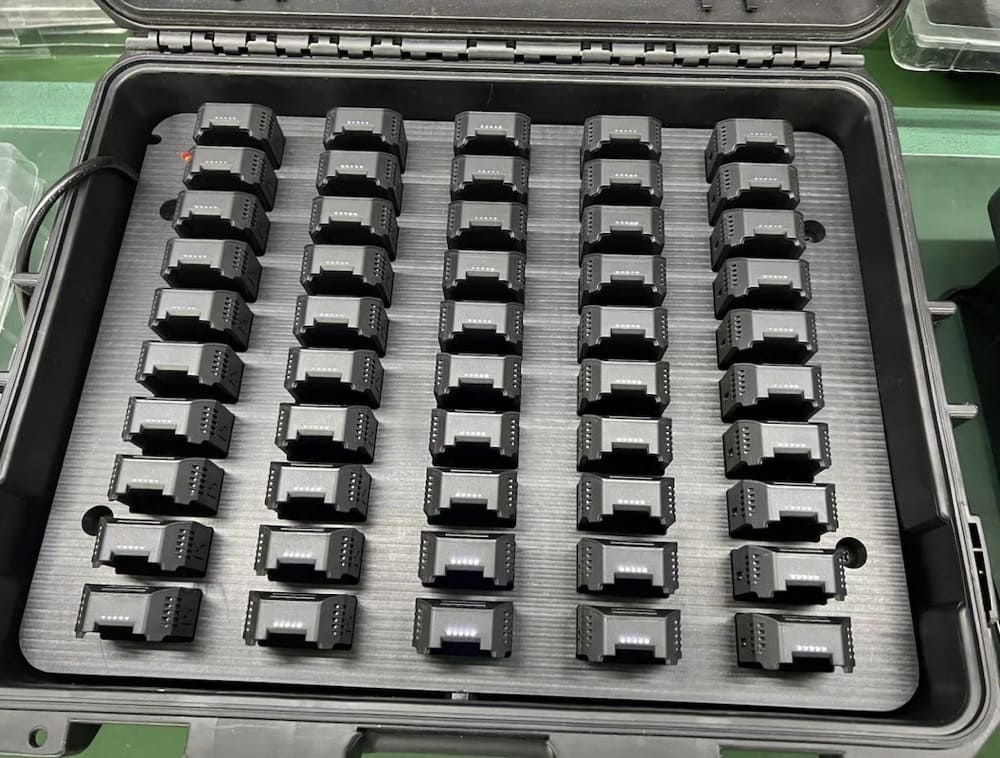
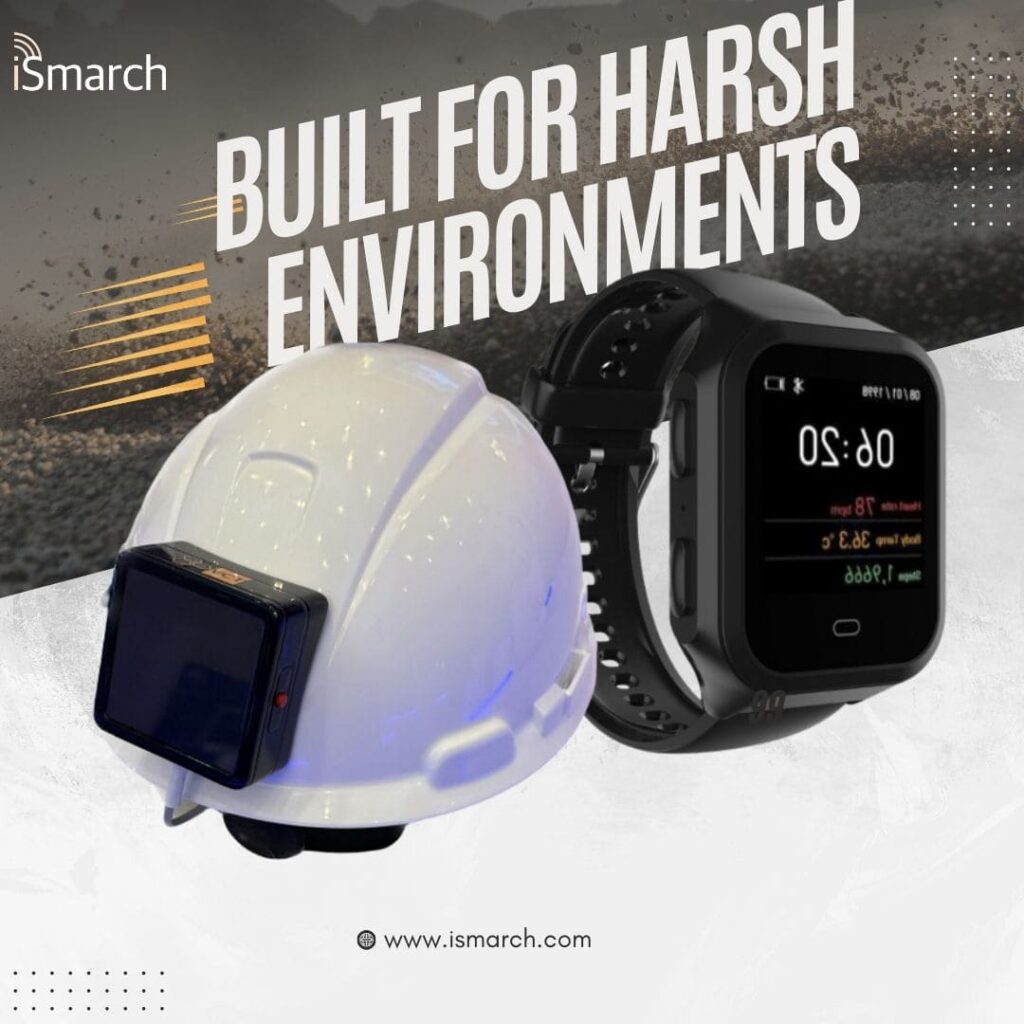
Long-Lasting Durability and Efficiency
Built to endure extreme conditions, both devices are ready to meet the rigorous demands of oil and gas work environments, ensuring reliable performance and long-lasting service.
The Benefits of Using Smart Wearables in the Oil & Gas Industry
Smart wearables, such as iSmarch’s J3 LoRaWAN Smartwatch and Smart Helmet Attachment (VCT lnSite), bring a range of benefits that go beyond traditional sensor-based predictive maintenance systems. In high-risk industries like oil and gas, where safety and efficiency are paramount, these devices offer unique advantages, creating a comprehensive safety and operational ecosystem that supports worker well-being, optimizes workflows, and enhances maintenance effectiveness.
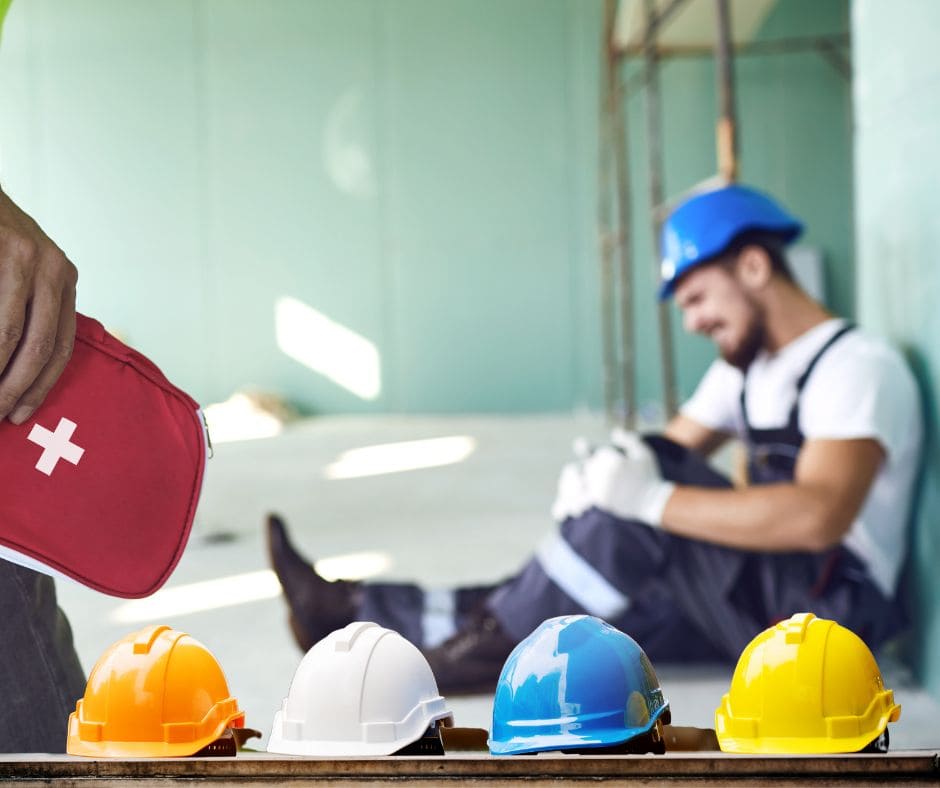
Enhanced Worker Safety and Health Monitoring
Real-Time Health Alerts
Wearables such as the J3 smartwatch continuously track vital signs, including heart rate, body temperature, and blood oxygen levels. If any metrics reach unsafe levels, supervisors receive instant alerts, enabling immediate response.
Environmental Hazard Awareness
While the J3 doesn’t have built-in environmental sensors, it acts as a hub, receiving alerts from other environmental sensors nearby, such as those that monitor toxic gas levels or extreme temperatures. This integration ensures that workers are kept safe from environmental risks.
Stress and Fatigue Monitoring
With HRV-based algorithms, the J3 smartwatch detects early signs of stress or fatigue. In the oil and gas industry, where long shifts and physical demands are the norm, this data helps supervisors ensure that workers are fit to handle tasks, reducing the risk of errors or injuries.
Increased Maintenance Efficiency and Reduced Downtime
Targeted Maintenance Alerts
Vibration and pressure sensors detect machinery anomalies, triggering alerts that can be sent directly to the J3 smartwatch, allowing nearby workers to quickly respond and assess the situation. This helps maintenance teams address specific issues as they arise, avoiding unnecessary inspections and keeping operations running smoothly.
Improved Maintenance Scheduling
By combining worker data from wearables and equipment data from sensors, maintenance teams can better prioritize tasks based on real-time conditions, optimizing scheduling and minimizing disruption.
Remote Monitoring and Analysis
Both the J3 smartwatch and the VCT lnSite helmet attachment transmit data to the cloud via LoRaWAN, enabling remote monitoring of both equipment and worker health. This centralized data provides a clearer overview of operational conditions and enables predictive maintenance without requiring physical presence, which is especially beneficial for remote or offshore sites.
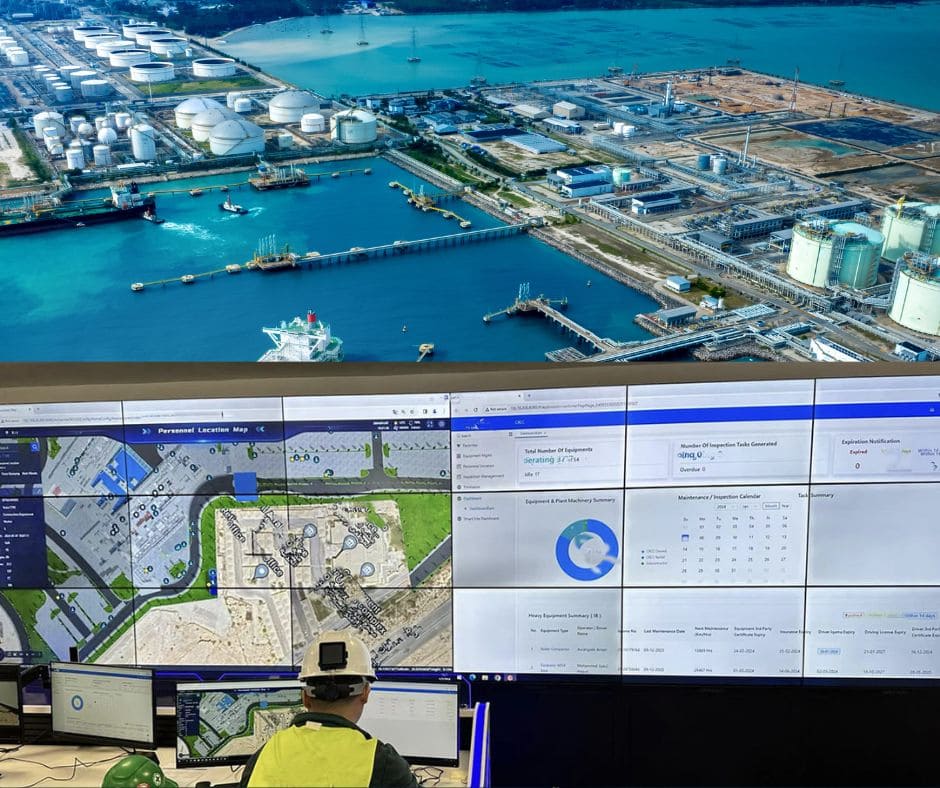
نبذة عن iSmarch
As a leader in smart wearable technology, iSmarch is dedicated to developing high-quality solutions that cater to the demanding environments of industries like construction site, mining, oil and gas, and more IoT specific sectors. Our J3 LoRaWAN Smartwatch و VCT lnSite Helmet Attachment are specifically designed to provide reliable, real-time data on worker health and safety, offering a level of operational control that traditional maintenance systems cannot achieve alone.
At iSmarch, we understand that each company’s needs are unique, especially in the diverse environments of the oil and gas sector. That’s why we offer comprehensive customer support and customization options to ensure our solutions fit seamlessly into your operations.
Tailored Solutions and Customization: iSmarch’s wearables can be customized to align with specific project needs, from adjusting sensor configurations to integrating with custom software.
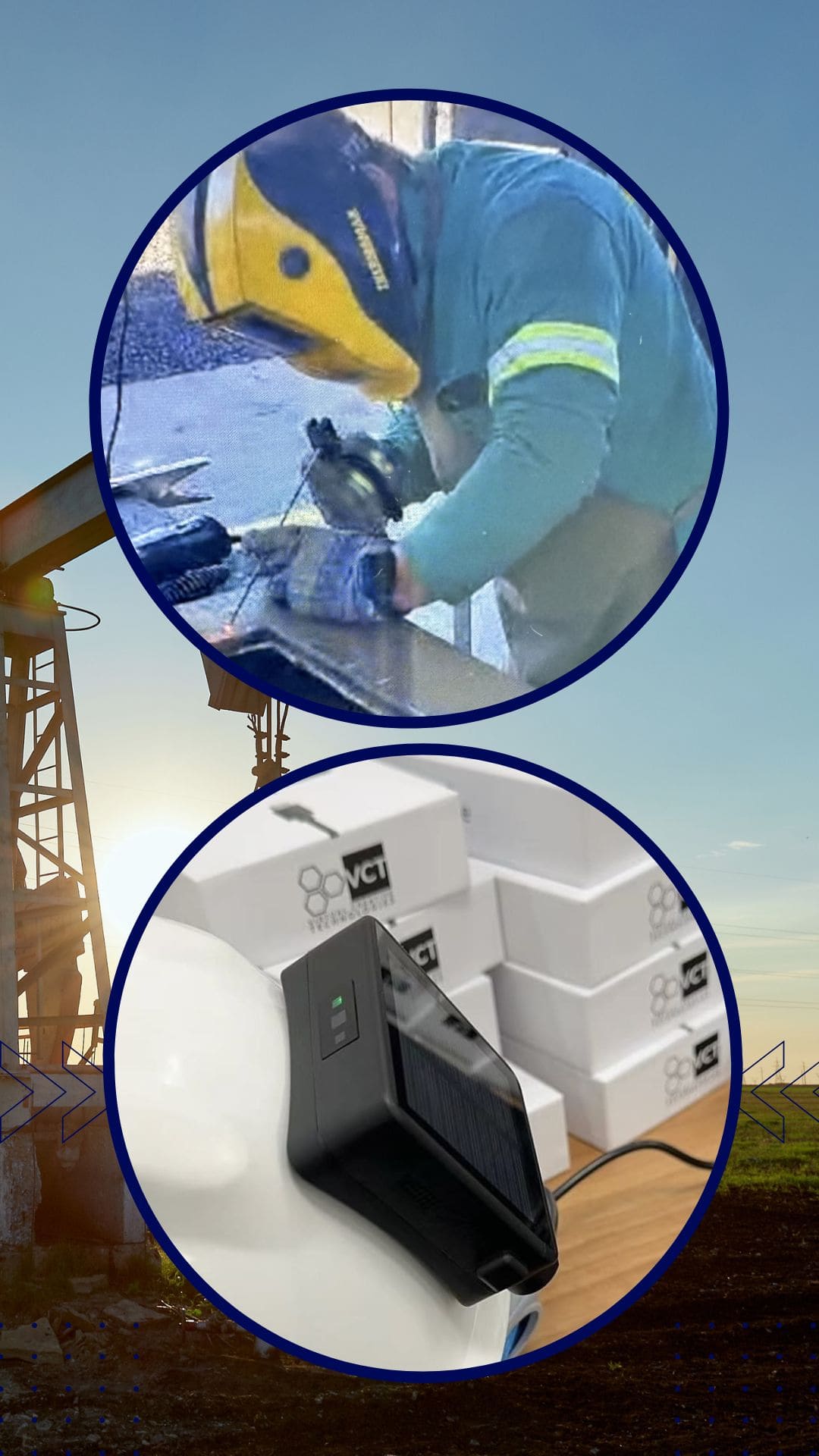
Customization Options and Open Device
لدينا J3 smartwatch و خوذة ذكية offer a high degree of customization, allowing companies to tailor these devices to meet the specific needs of their oil and gas projects. This flexibility makes our wearables the ideal solution for a wide range of safety and operational requirements.
الأسئلة الشائعة
Smart wearables, like iSmarch’s J3 LoRaWAN Smartwatch and VCT lnSite Helmet Attachment, complement traditional predictive maintenance systems by monitoring worker health, tracking their location, and receiving alerts from other sensors. This combination creates a connected ecosystem that helps prevent equipment failures, ensures worker safety, and enables faster response times when maintenance is required.
iSmarch’s wearables have the potential to work with existing sensor networks, but integration may require customization. If your sensors use Bluetooth, we would need access to their Bluetooth protocols to assess compatibility and explore potential modifications to our wearables for connection. This integration option can be discussed with our technical team to determine the feasibility and steps required for seamless operation with your existing predictive maintenance setup.
Absolutely. Both the J3 smartwatch and VCT lnSite helmet attachment are built to withstand harsh conditions commonly found in oil and gas operations. The J3 is IP68-rated for dust and water resistance, while the helmet attachment is made from high-stress materials that can endure temperatures up to 80°C and is also water-resistant. which allows for low-power, long-range communication even in remote areas with limited connectivity. The solar-powered helmet also ensures continuous operation without relying on external power sources, making it ideal for remote oil and gas sites.
The J3 smartwatch transmits vital signs and GPS data to the cloud every five minutes by default. This frequency can be adjusted based on specific project requirements or operational needs, ensuring that supervisors always have the most current information on worker health and safety.